한국원자력연구원, 3D 레이저 프린팅 기술 활용 20배 빠르게
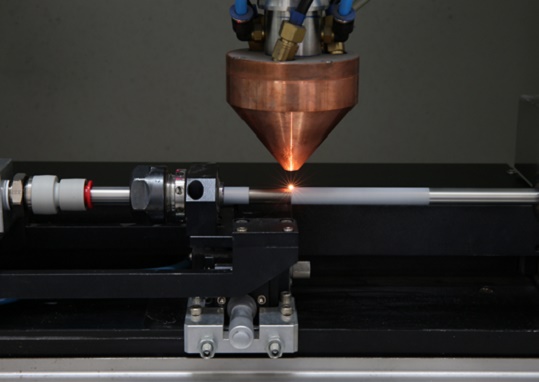
파이프에 산화물을 도포한 후 3D 프린터 레이저를 조사하는 모습
[대전=일요신문]육심무 기자 = 한국원자력연구원은 항공기 엔진이나 가스 터빈 부품과 같이 고온의 열을 견뎌야만 하는 핵심 부품 소재를 3D 레이저 프린팅 기술을 활용해 20배나 빠르게 만들 수 있는 기술을 세계 최초로 국내에서 개발했다.
5일 원자력연구원에 따르면 산화물 분산강화 합금을 만들 수 있는 이 기술은 원천성을 인정받아 현재 국내를 포함 미국, 일본, 유럽(프랑스)에 특허 등록을 완료한 상태다.
기존 산화물 분산강화 기술은 금속과 산화물을 파우더 형태로 만들어 혼합한 후 추가적인 복잡한 공정을 거쳐 만들기 때문에 많은 시간과 비용이 소요됐다.
또 최종 제품을 제작하기 위해서는 이미 강화 공정을 거쳐 강도가 크게 증가된 합금을 재료로 쓸 수밖에 없어 사용자가 원하는 형태의 제품을 만드는데 적잖은 어려움이 있었다.
원자력연구원에서 개발한 신기술은 최종 제품을 만든 후 제품 금속 표면에 산화물 입자를 도포하고 3D 프린터의 레이저 열원으로 금속을 녹이면서 동시에 산화물 입자를 혼합, 냉각해 금속 내부에 내열층을 만들어내는 방식이다.
산화물 입자를 금속 내부에 고루 분포시키면서 가공 시간과 비용을 기존 기술 대비 20분의 1로 단축할 뿐 아니라, 사용자가 원하는 특정 부분만 강화할 수 있는 혁신적인 기술로 평가받는다.
이번에 개발한 ‘3D 레이저 프린팅 기반 산화물 분산강화 기술’은 후쿠시마 원전 사고와 같은 원자로 수소 폭발을 방지하기 위해 개발을 시작했다.
후쿠시마 사고 당시 원자로 내부의 고온으로 핵연료 피복관이 변형·파괴되고 핵연료 피복관이 산화되면서 다량의 수소가 발생, 결국 수소 폭발로 이어졌다.
그러나 ‘3D 레이저 프린팅 기반 산화물 분산강화 기술’을 적용해 제작한 핵연료 피복관은 1200℃의 고온에서도 거의 변형되지 않기 때문에(기존 대비 4분의 1 이하), 사고 발생시 수소 발생을 크게 억제해 후쿠시마 사고와 같은 심각한 사고로 진행되지 않게 한다.
이에 사고 대응시간을 추가로 확보할 수 있어 사고시 핵연료의 안전성을 5배 정도 강화할 수 있을 것으로 평가된다.
핵연료 피복관 시장만으로도 국내 연 500억원, 세계시장 연 1조원 규모로 파악돼 이 기술이 상용화되면 내열 금속의 수입대체 및 수출 효과가 클 것으로 기대된다.
ilyo08@ilyo.co.kr