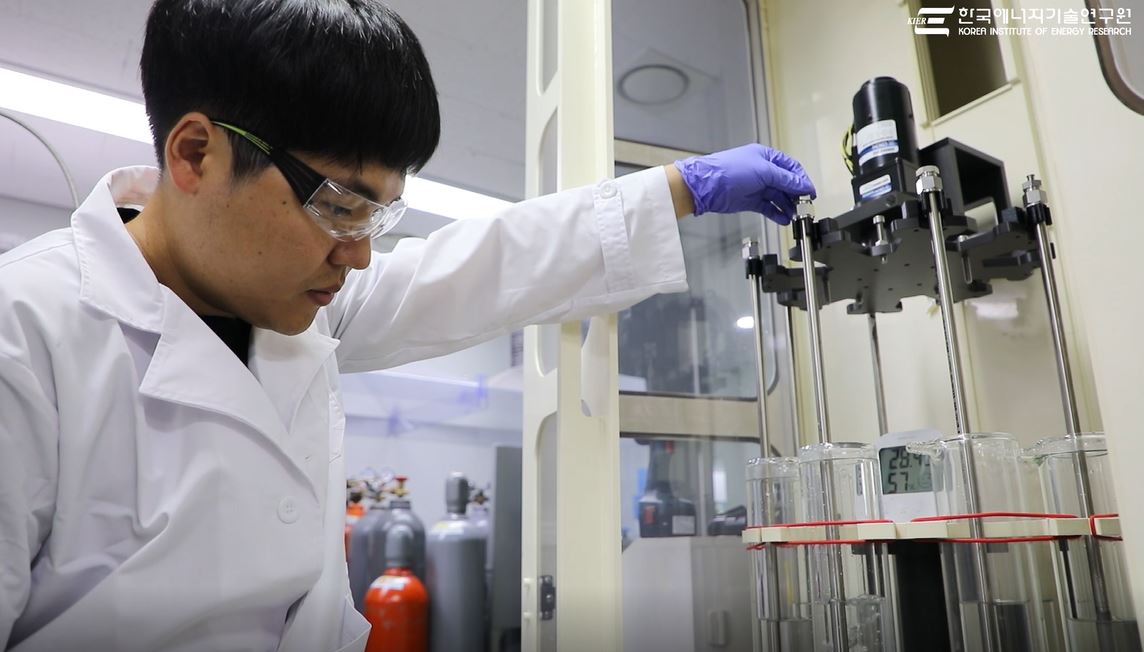
[대전=일요신문] 육군영 기자 = 천연가스, 바이오매스를 포함한 합성가스에서 고순도 수소를 생산하고 정제할 수 있는 기술이 국내 연구진에 의해 개발됐다.
한국에너지기술연구원(원장 곽병성)은 20일 천연가스, 바이오매스, 수전해 등 수소 생산 방식과 결합해 기존 기술의 문제를 극복하고 효율적으로 수소를 생산 및 정제할 수 있는 ‘복합막 형태의 팔라듐 분리막 기반 수소 생산·정제 핵심 기술’을 개발하는 데 성공했다고 발표했다.
현재 널리 이용되는 천연가스 기반 수소생산 기술은 촉매반응을 적용한 메탄 수증기 변환 방식이다. 그러나 이 방식은 700~900℃의 고온에서 운전되기 때문에 열내구성이 우수한 소재로 구성해야 하고, 분리 공정과 후속 정제 공정이 분리돼 넓은 설치장소와 많은 설치비용이 소요된다.
반면에 에너지연이 개발한 기존의 메탄 수증기 변환 방식에 팔라듐 분리막을 활용하면 500~550℃의 낮은 온도에서도 운전이 가능하다. 또 별도의 정제 공정을 추가하지 않아도 합성가스 중 수소만을 선택적으로 분리·정제해 보다 높은 효율로 고순도 수소를 생산할 수 있다.
아울러 합성가스에서 수소만 분리해내기 때문에 남아있는 이산화탄소를 보다 쉽게 포집할 수 있어 온실가스 감축과 친환경에너지 확산에도 기여할 수 있다.
팔라듐 분리막은 포일형태의 분리막과 다공성지지체 위에 박막의 팔라듐을 코팅하는 복합막으로 나뉜다.
포일형태의 분리막은 이미 상용화됐으나 두께가 두꺼워 단가가 높고, 수소투과도가 낮다는 단점이 있다. 이에 비해 복합막은 팔라듐 두께를 얇게 형성할 수 있으나 팔라듐을 수소만 투과하게끔 코팅하는 것은 매우 어려운 실정이다.
연구진은 팔라듐 분리막 코팅 공정의 핵심인 ‘무전해도금법’을 독자적으로 개발했다.
이 기술을 이용하면 도금액 내에 포함된 팔라듐을 기존의 방식보다 10% 가량 높은 99.5% 이상 활용할 수 있으며, 현재 판매되고 있는 팔라듐 포일막 대비 3~5배 낮은 5㎛(마이크로미터) 이하의 두께로 코팅해도 우수한 수소 정제가 가능하다.
또 확산방지막 코팅 기술인 ‘블로윙 코팅기술’을 함께 개발해 원통형 금속 표면에 100㎛(머리카락 두께의 1000분의 1) 이하의 매우 얇은 세라믹 막을 단순하면서도 균일하게 코팅하는 데 성공, 이를 통해 전체 분리막의 안정성과 경제성을 개선했다.
연구진은 개발된 핵심 기술을 바탕으로 직경 1인치, 길이 45㎝의 팔라듐 분리막을 제조하는데 성공했으며, 분리막이 적용된 10N㎥/h(시간당 뉴턴세제곱미터)급 수소정제기도 개발했다.
이 내용은 분리막 전문 국제학술지인 저널 오브 멤브레인 사이언스(Journal of Membrane Science) 등에 게재돼 학술적 가치를 인정받았다.
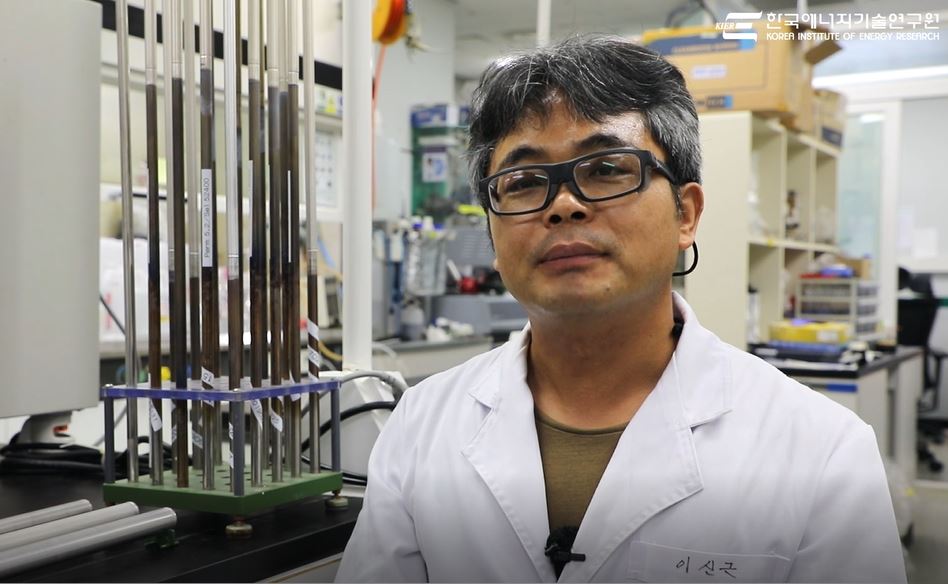
한국에너지기술연 이신근 책임연구원
이신근 책임연구원은 “팔라듐 분리막 수소 생산·정제 기술은 기존 화석연료 기반 수소 생산 방식에 접목해 효과적으로 반응효율을 증진시킬 수 있는 기술”이라며 “향후 재생에너지 및 친환경에너지원을 이용한 수소 생산방식에서 효율 향상을 위해 핵심적으로 적용할 수 있으며, 특히 현지공급형(On-Site) 고순도 수소 생산·정제 분야에서 중요한 역할을 할 것으로 기대한다”고 밝혔다.
연구진은 향후 팔라듐 분리막 기반 수소 추출 공정 효율 향상을 위한 모듈화 기술과 시스템 구성 기술을 전문적으로 확보할 예정이다. 이를 통해 천연가스를 비롯한 화석연료 및 바이오매스를 기반으로 한 수소 생산용 중·소형급 수소플랜트 개발과 수전해 등에 적용가능한 수요 맞춤형 수소정제기를 규격화하고 국내·외 다양한 산업분야에 대응할 계획이다.
ilyo08@ilyo.co.kr