지역기업 대상 제조 AI 적용 통해 ‘제품 품질 향상’, ‘업무 효율성 증대’, ‘작업환경 개선’ 등 기대
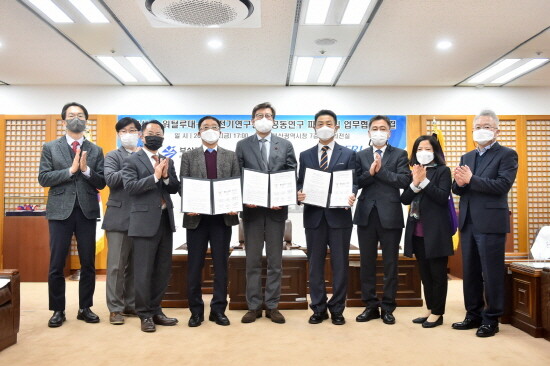
이어 12월에는 KERI와 부산광역시, 캐나다 워털루대학이 지역에서의 AI 저변 확대를 위한 공동연구 파트너십 업무협약을 체결하기도 했다. 이러한 후속조치로 올해부터 부산광역시 2개 기업(㈜대양볼트, 태화정밀공업(주))의 제조 현장에 AI 기술 도입을 시작한다.
자동차 부품 및 장비 생산 전문 업체인 ㈜대양볼트에는 빅데이터 기반의 ‘자동화 고주파 열처리 AI 기술’이 적용 및 구축된다. 기존 사람이 행하던 고주파 열처리 과정은 유독가스 발생으로 인한 건강 문제, 고전압에 대한 감전 및 고열로 인한 화상 문제, 열처리 품질 확보의 불확실성, 작업 데이터 관리의 부재 등 많은 어려움이 발생했다.
하지만 올해부터는 협동 로봇이 사람 대신 현장에 투입되고, 현장의 열처리 변수(파라미터)를 기반으로 학습된 AI가 온도·주파수·전압·시간 등 상황에 따라 제품 경도의 최적화 열처리를 수행한다. 업무 효율성 향상은 물론, 산업 안전 및 근로 환경 개선에도 큰 역할을 하는 것이다. 수치적으로 환산하면 연간 기대효과는 제품 불량률 감소 및 검사 작업시간 단축 등 약 1억 7천만원에 달한다.
또 다른 기업인 태화정밀공업(주)에는 자동차 및 중장비 부품을 생산하는 과정에서 가장 중요한 정밀가공 공정라인에 ‘AI 공구관리 기술’이 적용된다. 기존에는 작업자의 경험과 감각에 의존하다 보니 공구에 문제가 발생하더라도 즉시 감지가 불가능하고, 작업을 마친 후에야 제품의 불량을 인지하고 역으로 추적해 공구 문제를 발견하는 상황이었다. 이로 인한 재료 및 시간 손실, 재작업(rework)에 따른 불량률·제조원가 상승, 생산성 하락 등 어려움이 있었다.
그러나 이제부터는 AI를 기반으로 공구의 상태를 사전에 진단하고 파손을 감지할 수 있는 시스템을 구축하고, 이를 생산라인에 적용해 가공 공정에서의 품질 혁신을 기대할 수 있게 됐다. 생산 데이터도 축적해 공구의 수명까지 예지하고, 적절한 시기에 공구가 미리 교체될 수 있도록 만들어 준다. 이러한 제조 AI를 통한 기대효과는 공구비/인건비/재작업비 절감 등 연간 약 2억 8천만원에 달한다.
KERI 김종문 인공지능연구센터장은 “우리의 사업은 AI를 제조업에 응용해 기업의 업무 효율성과 생산성, 제품의 품질 향상 및 현장의 안전·환경 개선을 도모하는 것이며, 이를 통해 지역 산업 경쟁력을 높이고, 일자리 창출에 기여하는 데 목적이 있다”며 “올해 부산 지역에서의 제조 AI의 대표 모델 공장이 될 2개 기업에 이어, 점진적으로 AI의 적용범위, 수혜기업 등을 확대해 나가겠다”고 전했다.
이혜림 부산/경남 기자 ilyo33@ilyo.co.kr